BAMBOO REINFORCED CONCRETE CONSTRUCTION
February 1966
U. S. NAVAL CIVIL ENGINEERING LABAORATORY
Port Hueneme, California
By
Francis E. Brink and Paul J. Rush
ABSTRACT
This report has been prepared to assist field personnel in the design and construction of bamboo reinforced concrete. The information in this report has been compiled from reports of test programs by various researchers and represents current opinion.
Comments on the selection and preparation of bamboo for reinforcing are given. Construction principles for bamboo reinforced concrete are discussed. Design procedures and charts for bamboo reinforced concrete are given and conversion methods from steel reinforced concrete design are shown. Six design examples are presented.
EDITOR'S NOTES - DECEMBER 2000
NOTE: This document was originally a publication of the U.S. Naval Civil Engineering Laboratory. We have placed this document on the web because of its historical interest to those interested in the topic of alternative methods of concrete construction. These notes were added after this document was entered into a modern word processor and are not part of the original document.
DISCLAIMER: This document was scanned and retyped from a hard copy of the original that was about 35 years old. No effort has been made to verify the correctness of information or calculations contained herein, and the reader takes all responsibility when applying this information in his or her work. It is possible there is more recent research and studies that supercede the material contained in this study. Use this information at your own risk. No one at romanconcrete.com or its associates takes any responsibility as to the fitness of this material for use in actual construction. This study is being shared for research use only.
CHANGES: The only changes to the original document, besides these notes and the formatting changes available in a modern word processor, (besides potential mistakes in typing) are purely formatting and include the addition of a table of contents, numbering of sections, a list of tables and figures, and the change from table I in the original document to table II in this document. Please report all mistakes in this document to:
RECOGNITION: Recognition is given to Rear Admiral Jack E. Buffington, Naval Facilities Engineering Command, United States Navy, Retired, for his encouragement in placing this unusual article on bamboo concrete construction on the internet. It identifies the potential for an alternative light construction method at low cost for areas where steel reinforcement might be prohibitive. In this case, bamboo might replace steel in light construction as the tensile element in concrete design. This report highlights the technical expertise that exists in the Navy's Civil Engineering Corps and the personnel at the Naval Civil Engineering Laboratory, Port Hueneme, California in particular. Their willingness to share such creative information with the world is truly creditable and appreciated.
Contents
Tables
Figures
1. INTRODUCTION
The use of bamboo as reinforcement in portland cement concrete has been studied extensively by Clemson Agricultural College.(ref 1) Bamboo has been used as a construction material in certain areas for centuries, but its application as reinforcement in concrete had received little attention until the Clemson study.
A study of the feasibility of using bamboo as the reinforcing material in precast concrete elements was conducted at the U. S. Army Engineer Waterways Experiment Station in 1964.(ref 2) Ultimate strength design procedures, modified to take into account the characteristics of the bamboo reinforcement were used to estimate the ultimate load carrying capacity of the precast concrete elements with bamboo reinforcing.
Bamboo was given recent consideration for use as reinforcement in soil-cement pavement slabs in which the slabs behave inelastically even under light loads. For this case ultimate load analysis was shown to be more economical and suitable for use.(ref 3)
The results of these investigations form the basis of the conclusions and recommendations presented in this report. Further studies will be required before complete confidence can be placed theoretical designs based on the material presented here.
2. SELECTION AND PREPARATION OF BAMBOO
2.1 Selection
The following factors should be considered in the selection of bamboo culms (whole plants) for use as reinforcement in concrete structures:
- Use only bamboo showing a pronounced brown color. This will insure that the plant is at least three years old.
- Select the longest large diameter culms available.
- Do not use whole culms of green, unseasoned bamboo.
- Avoid bamboo cut in spring or early summer. These culms are generally weaker due to increased fiber moisture content.
2.2 Preparation
Sizing. Splints (split culms) are generally more desirable than whole culms as reinforcement. Larger culms should be split into splints approximately 3/4 inch wide. Whole culms less than 3/4 inch in diameter can be used without splitting. (See Fig 4)
Splitting the bamboo can he done by separating the base with a sharp knife and then pulling a dulled blade through the culm. The dull blade will force the stem to split open; this is more desirable than cutting the bamboo since splitting will result in continuous fibers and a nearly straight section. Table II shows the approximate net area provided by whole culms and by 3/4-inch-wide splints, as well as the cross-sectional properties of standard deformed steel bars and wire mesh.
Seasoning. When possible, the bamboo should be cut and allowed to dry and season for three to four weeks before using. The culms must be supported at regular spacings to reduce warping.
Bending. Bamboo can be permanently bent if heat, either dry or wet, is applied while applying pressure. This procedure can be used for forming splints into C-shaped stirrups and for putting hooks on reinforcement for additional anchorage.
Waterproof Coatings. When seasoned bamboo, either split or whole, is used as reinforcement, it should receive a waterproof coating to reduce swelling when in contact with concrete. Without some type of coating, bamboo will swell before the concrete has developed sufficient strength to prevent cracking and the member may be damaged, especially if more than 4 percent bamboo is used. The type of coating will depend on the materials available. A brush coat or dip coat of asphalt emulsion is preferable. Native latex, coal tar, paint, dilute varnish, and water-glass (sodium silicate) are other suitable coatings. In any case, only a thin coating should be applied; a thick coating will lubricate the surface and weaken the bond with the concrete.
3. CONSTRUCTION PRINCIPLES
In general, techniques used in conventional reinforced concrete construction need not he changed when bamboo is to be used for reinforcement.
3.1 Concrete Mix Proportions
The same mix designs can be used as would normally be used with steel reinforced concrete. Concrete slump should be as low as workability will allow. Excess water causes swelling of the bamboo. High early-strength cement is preferred to minimize cracks caused by swelling of bamboo when seasoned bamboo cannot be waterproofed.
3.2 Placement of bamboo
Bamboo reinforcement should not be placed less than 1-1/2 inches from the face of the concrete surface. When using whole culms, the top and bottom of the stems should be alternated in every row and the nodes or collars, should be staggered. This will insure a fairly uniform cross section of the bamboo throughout the length of the member, and the wedging effect obtained at the nodes will materially increase the bond between concrete and bamboo.
The clear spacing between bamboo rods or splints should not be less than the maximum size aggregate plus 1/4 inch. Reinforcement should be evenly spaced and lashed together on short sticks placed at right angles to the main reinforcement. When more than one layer is required, the layers should also be tied together. Ties should preferably be made with wire in important members. For secondary members, ties can be made with vegetation strips.
Bamboo must be securely tied down before placing the concrete. It should be fixed at regular intervals of 3 to 4 feet to prevent it from floating up in the concrete during placement and vibration. In flexural members continuous, one-half to two-thirds of the bottom longitudinal reinforcement should be bent up near the supports. This is especially recommended in members continuous over several supports. Additional diagonal tension reinforcement in the form of stirrups must be used near the supports. The vertical stirrups can be made from wire or packing case straps when available; they can also be improvised from split sections of bamboo bent into U-shape, and tied securely to both bottom longitudinal reinforcement and bent-up reinforcement. Spacing of the stirrups should not exceed 6 inches.
3.3 Anchorage and Splicing of Reinforcements
Dowels in the footings for column and wall reinforcement should be imbedded in the concrete to such a depth that the bond between bamboo and concrete will resist the allowable tensile force in the dowel. This imbedded depth is approximately 10 times the diameter of whole culms or 25 times the thickness of 3/4 inch wide splints. In many cases the footings will not be this deep; therefore, the dowels will have to be bent into an L-shape. These dowels should be either hooked around the footing reinforcement or tied securely to the reinforcement to insure complete anchorage. The dowels should extend above the footings and be cut so that not more than 30 percent of the splices will occur at the same height. All such splices should be overlapped at least 25 inches and be well tied.
Splicing reinforcement in any member should be overlapped at least 25 inches. Splices should never occur in highly stressed areas and in no case should more than 30 percent of the reinforcement be spliced in any one location.
4. DESIGN PRINCIPLES
Bamboo reinforced concrete design is similar to steel reinforcing design. Bamboo reinforcement can be assumed to have the following mechanical properties:
Table I. Mechanical properties of bamboo reinforcement
Mechanical Property | Symbol | Value (psi) |
Ultimate compressive strength | | 8,000 |
Allowable compressive stress | s | 4,000 |
Ultimate tensile strength | | 18,000 |
Allowable tensile stress | s | 4,000 |
Allowable bond stress | u | 50 |
Modulus of elasticity | E | 2.5x106 |
When design handbooks are available for steel reinforced concrete, the equations and design procedures can be used to design bamboo reinforced concrete if the above mechanical properties are substituted for the reinforcement.
Due to the low modulus of elasticity of bamboo, flexural members will nearly always develop some cracking under normal service loads. If cracking cannot be tolerated, steel reinforced designs or designs based on unreinforced sections are required.
Experience has shown that split bamboo performs better than whole culms when used as reinforcing. Better bond develops between bamboo and concrete when the reinforcement is-split in addition to providing more compact reinforcement layers. Large-diameter culms split into 3/4-inch- wide splints are recommended. (References to splints in the following examples will be understood as meaning 3/4-inch-wide splints of a specified thickness unless otherwise stated.
Design principles for the more common structural members are presented in the following sections. Examples of the use of these principles for each member discussed are included.
4.1 Beams and Girders
Flexural members reinforced with bamboo can be designed with the use of Figure 1. Bamboo longitudinal reinforcement should be between 3 and 4 percent of the concrete cross section.
Figure 2 can be used to convert existing designs for steel reinforced beams to equivalent bamboo reinforced designs. The curve provides the cross-sectional dimensions of a bamboo reinforced beam that will have the same bending moment resistance coefficient as a balanced steel reinforced beam, singly reinforced. Economy of concrete increases going to the left on the curve; therefore, deeper, narrower replacement beams are recommended.
The number and size of bamboo reinforcing rods (culms or splints) can be selected from Figure 2b. These curves are drawn for 3 percent of the concrete cross section as bamboo reinforcement which is in the optimum range for flexural members. Other reinforcement percentages can be used as noted on the figure. A minimum number of rods should be used to provide adequate spacing. The bamboo stirrup area should always be about 4 times the steel stirrup area.
4.1.1 Example 1 - Design of Bamboo Reinforced Beam:
Design a bamboo reinforced concrete beam to span 8 feet and to carry a uniform dead load plus live load of 500 pounds per linear foot and two concentrated loads of 12,000 pounds each symmetrically located 2 feet each side of the center line of span. Assume the ultimate strength of the concrete is 2500 psi; the allowable compression stress is 0.45 f'
c or 1125 psi. Allowable unit diagonal tension stress,

, in the concrete is 0.03 f'
c or 75 psi. Allowable tension stress,
s, in the bamboo is 4000 psi; the allowable unit bond stress between bamboo and concrete is 50 psi.
1. At the intersection of the allowable stress curves (Figure 1) for concrete and bamboo, find R = 115 and p = 3.1 percent.
2. Maximum bending moment, M, is given by:

3. From
bd2 = 336,000/115 = 2920 in.3
4. If b = 8 in. is chosen, then d = (2920/8)
1/2 = 19.1 in. 5. Bamboo reinforcement = pbd = 0.031(8)(19.1) = 4.75 sq in.
6. Use 3/4-inch-thick splints, area = 0.563 sq in. (from Table II). Number required = 4.75/0.563 = 8.4; round up to 9. Space evenly in three rows. Bend up top row randomly in the outer one-third ends of the beam.
7. Check the bond stress. Maximum shear at the support, V, is determined as:
The perimeter of one splint is 4(3/4) or 3 in.; the total perimeter of the longitudinal reinforcement,
, is 9(3) = 27 in. The value of j = 0.925 is taken from Figure 1 for 3.1 percent reinforcement. The bond stress, u, is calculated from:
This is less than the allowable bond stress of 50 psi.
8. Calculate the shear, V', taken by the concrete from
Where
is the allowable diagonal tension stress of the concrete. 9. Try 1/4-inch-thick splints for stirrups. The area provided by one stirrup bent into a U-shape, A, is 2(0.1875) = 0.375 sq. in. Maximum spacing, s, is given by:

Common practice is to include two additional stirrups past the point where diagonal tension reinforcement is not needed. 4.1.2 Example 2 - Replacement of a Steel Reinforced Beam with a Bamboo Reinforced Beam:
Construction drawings call for the beam given in the sketch below. Replace it with a bamboo reinforced beam. There are no objections to deepening the member.
1. Select the cross-sectional dimensions from Figure 2a. Avoid using sections with depth to width ratios greater than 4 for reasons of stability. Try width of 1.0b or 10 in. and a depth of 1.32d or 29.0 in. The area is 290 sq in.
2. The amount of reinforcement can be selected from Figure 2b. Assume that 3/4-inch-thick splints will be used. The number of splints required for 200 sq in. is determined at 11. This number is multiplied by the ratio 290/200 to get 16 splints. These should be-distributed evenly in four rows.
3. Determine the vertical stirrups required. The No. 4 steel stirrups have a cross-sectional area of 0.2 sq in. (Table II). These stirrups are spaced at 10 in. which provides (12/10)(0.2)= 0.24 sq in. of reinforcement in a 12-inch length. Four times this area should be used for bamboo stirrups or 0.96 sq in. per foot of length. From Figure 4, select 3/8-inch-thick splints spaced at 4-inch centers.
4. The top two rows should be bent up randomly in the outer one-third sections of the beams to assist the vertical stirrups in resisting diagonal tension.
The final design is shown in the following sketch.
4.2 Columns
Bamboo reinforcement in columns serves to resist a compression load equal to that taken by the concrete it displaces; it also will resist shear and tensile stresses. Of the full cross section of concrete, only 80 percent is considered effective in rectangular tied, columns. Allowable concrete stress should not exceed 0.225 f'
c where f'
c is the ultimate compressive strength of the concrete.
Vertical reinforcement should be approximately 4 percent of the column cross section for rectangular columns. When bamboo is used as lateral tie reinforcement, the ties should be spaced not over 16 times the least dimension of the vertical reinforcement nor farther apart than the least dimension of the column. Enough ties should be provided so that every vertical bar is held firmly in its designed position and has lateral support equivalent to that provided by a 90-degree corner of a tie. A common rule for determining the size of a tie is that its cross-sectional area is 2 percent of the area of all the vertical reinforcement confined by it.
The concrete cross-sectional area of bamboo reinforced rectangular columns conservatively should be 2.25 times the concrete area of steel reinforced rectangular columns, indicating a 50-percent increase in face dimensions.
4.2.1 Example 3 - Square Bamboo Reinforced Column Design:
Determine the cross section and bamboo reinforcement of a column required to carry an axial load of 70,000 lb. Ultimate compression strength of the concrete, f'
c, is 2500 psi.
1. For an unreinforced rectangular column the safe axial load, P, is given by:
P = 0.8Ag (0.225 f'c)
where Ag is the cross-sectional area of the concrete column.
2. The column should have a cross-sectional area of:

3. If a square column is chosen, it will have face dimensions of
b = (155.5)1/2 = 12.47 in., say 12.5 in.
4. The amount of vertical reinforcement should be 4 percent of the concrete area and can be obtained from Figure 2. Try 3/4-inch-thick splints. The number required is 8.8 for an area of (12.5)(12.5) = 156 sq in. However, Figure 2 provides only 3-percent reinforcement; thus 8.8 should be multiplied by (4/3) to get 11.7. Thus, 12 splints should be used; these should be spaced evenly around the perimeter with 1-1/2 in. of cover. Lateral ties should be arranged as shown in the following figure to provide each vertical splint with a 90-degree corner (or smaller).
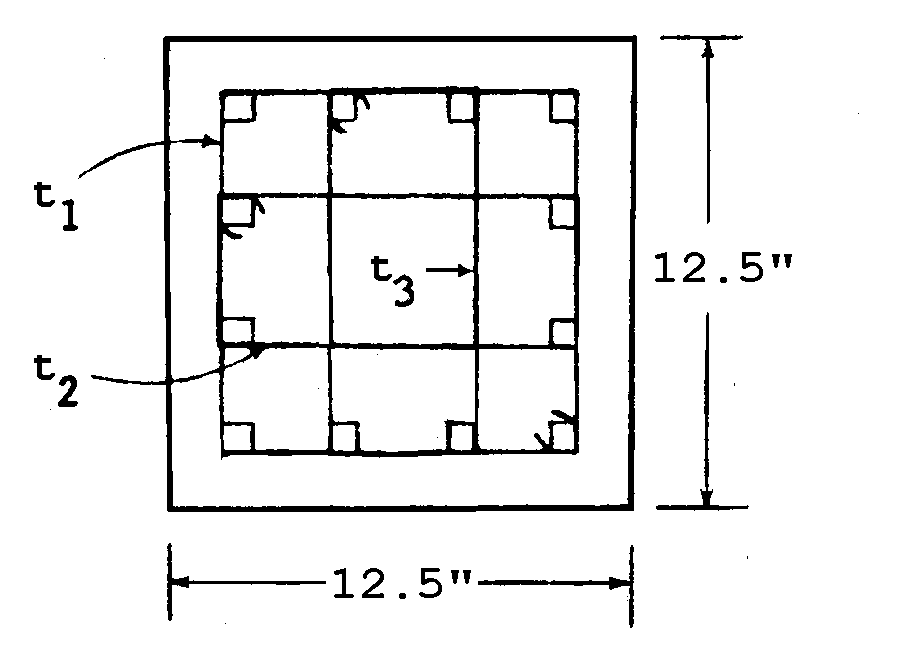
5. Tie reinforcement size should be 2 percent of the total area of the vertical bars confined by it. Each tie confines four vertical bars or an area of 4(3/4)(3/4) = 2.252 sq in. The cross-sectional area of the ties should be at least 2 percent of this or 0.02(2.252) = 0.045 sq in. Try 1/4-inch by 1/4-inch splints. The cross-sectional area is (1/4)(1/4) = 0.063 sq in. and therefore is adequate. The least dimension of the column is 12.5 in., and 16 times the thickness of the vertical reinforcement is 16(3/4) = 12.0 in.; therefore, spacing of the lateral ties is restricted to a maximum of 12 in.
4.2.2 Example 4 - Replacement of Steel Reinforced Square Column Design with Bamboo Reinforced Square Column:
Construction drawings call for a 12-inch-square concrete column reinforced with 12 No. 6 steel reinforcing bars. Three No. 2 ties on 12-inch centers are required. Replace this column with a square column reinforced and tied with bamboo.
1. The face dimensions should be increased by 50 percent. The bamboo reinforced column will have sides of 1.5(12) = 18.0 in.
2. The cross-sectional area is 18.0(18.0) = 324 sq in. Use 4 percent of the concrete area as vertical reinforcement. Figure 2 is used to determine the size and number of bamboo reinforcement. Assume 3/4-inch-thick splints will be used. For a concrete area of 200 sq in., the number of these splints required is 11.0. Since this figure provides 3-percent reinforcement, the number of splints should be multiplied by the ratio (4/3); it should also be multiplied by the ratio (324/200) as a correction factor for concrete area. These multiplications indicate that 24 splints should be used.
3. Lateral ties should be arranged as shown in the following figure. Tie reinforcement should be 2 percent of the area of the vertical bars confined by it. Each tie confines four 3/4-inch-thick splints; therefore, the calculations for tie size and spacing are identical to those in Example 3.
4.3 Ground-Supported Slabs
Figure 3 is used to determine slab thickness and required amount of bamboo reinforcement. Figure 4 can be used to determine the size and spacing of the reinforcement. In general, the reinforcement spacing should not be greater than the slab thickness.
When designs are available for steel reinforced slabs, no change in thickness is required when reinforced with bamboo instead of steel. However, the volume of the bamboo matting reinforcement should be about 4 times the amount used for steel matting.
4.3.1 Example 5 - Ground-Supported Slab Design:
Design a bamboo reinforced concrete slab to support a maximum wheel load of 7000 pounds. The wheel contact area on the slab is estimated at 60 sq in. Slab length between joints will be 8 ft.
1. The slab thickness is determined from Figure 3a to be about 5-1/2 in.
2. The required reinforcement is determined from Figure 3b to be 0.11 sq in. per foot of slab width.
3. The amount of the reinforcement is determined from Figure 4. The required amount of reinforcement can be provided by 1/8-inch-thick splints on 12-inch centers. However, in general, the reinforcing spacing should not be greater than the slab thickness; a 6-inch spacing is adequate.
4.3.2 Example 6 - Replacement of Steel Reinforced Slab with a Bamboo Reinforced Slab:
Construction drawings call for a 6-inch-thick slab reinforced with No. 10 gage steel reinforcing wire on 6-inch centers. Replace it with a bamboo reinforced slab.
1. The thickness of the slab does not change.
2. From Table II, the cross-sectional area of a No. 10 gauge wire is 0.0143 sq in. Since these wires are spaced at 6 in., the area per foot is 0.0286 sq in. Bamboo reinforcement should be 4 times that of the steel reinforcement or 0.114 sq in. per foot of slab width. From Figure 4, 1/8-inch-thick splints on 8-inch centers is adequate; however, the spacing should not exceed the slab thickness so a 6- inch spacing should be used.
4.4 Walls
Non-bearing concrete walls should have a thickness of not less than 5 inches and not less than 1/30 the distance between the supporting or enclosing members; they should be reinforced with at least 3/4-inch-diameter culms on 6-inch centers in both vertical and horizontal directions. This reinforcement should be provided as a one-layer mat in the middle of the wall. Two bamboo culms 1/2 inch or more in diameter should be placed above and at the sides of openings, and two 3/4-inch-diameter culms 4 feet long should be placed diagonally across the corners of openings.
5. REFERENCES
1. H. E. Glenn. "Bamboo reinforcement in portland cement concrete," Engineering Experiment Station, Clemson Agricultural College, Clemson, South Carolina, Bulletin No. 4, May 1950.
2. U. S. Army Engineer Waterways Experiment Station. Technical Report No. 6-646: "Precast concrete elements with bamboo reinforcement," by E. F. Smith and K. L. Saucier. Vicksburg, Mississippi, May 1964.
3. S. R. Mehra and R. G. Ghosh. "Bamboo-reinforced soil-cement," Civil Engineering and Public Works Review, Vol. 60, no. 711, October 1965; vol. 60, no. 712. November 1965.
4. "Concrete floors on ground," Portland Cement Association Concrete Information, ST-51.
5. American Concrete Institute. "Building code requirements for reinforced concrete," (ACI 318-56). May 1956.
6. Department of the Navy, Bureau of Yards and Docks. Design Manual NAVDOCKS DM-2, Structural Engineering. October 1964.
Figures and Tables
Figure 1. Resistance coefficients for bamboo reinforced concrete beams and their flexural members.
Figure 2. Bamboo substitute beams and reinforcement.
Figure 3. Slab thickness and reinforcement for ground supported slabs.
Figure 4. Size and spacing of bamboo reinforcement in slabs and walls.
Table II . Properties of bamboo and steel reinforcing bars
BAMBOO
Whole Culms |
Diameter (in.) | Area (sq. in.) |
3/8 | 0.008 |
1/2 | 0.136 |
5/8 | 0.239 |
3/4 | 0.322 |
1 | 0.548 |
2 | 1.92 |
3/4 Inch Wide Splints |
Thickness (in.) | Area (sq. in.) |
1/8 | 0.094 |
1/4 | 0.188 |
3/8 | 0.282 |
1/2 | 0.375 |
5/8 | 0.469 |
3/4 | 0.563 |
STEEL REINFORCING
Nominal Dimensions - Round Sections |
Bar Designation No. | Nominal Diameter (in.) | Cross Sectional. Area (sq. in.) |
2 | 0.250 | 0.05 |
3 | 0.375 | 0.11 |
4 | 0.500 | 0.20 |
5 | 0.625 | 0.31 |
6 | 0.750 | 0.44 |
7 | 0.875 | 0.60 |
8 | 1.000 | 0.79 |
9 | 1.128 | 1.00 |
10 | 1.270 | 1.27 |
11 | 1.410 | 1.56 |
STEEL WIRE
AS&W Wire Guage Numbers | Diameter (in) | Area (sq. in.) | Weight (lb/ft) |
0000 | 0.3938 | 0.12180 | 0.4l36 |
000 | 0.3625 | 0.10321 | 0.3505 |
00 | 0.3310 | 0.086049 | 0.2922 |
0 | 0.3065 | 0.073782 | 0.2506 |
1 | 0.2830 | 0.062902 | 0.2136 |
2 | 0.2625 | 0.054119 | 0.1838 |
3 | 0.2437 | 0.046645 | 0.1584 |
4 | 0.2253 | 0.039867 | 0.1354 |
5 | 0.2070 | 0.033654 | 0.1143 |
6 | 0.1920 | 0.028953 | 0.09832 |
7 | 0.1770 | 0.024606 | 0.08356 |
8 | 0.1620 | 0.020612 | 0.07000 |
9 | 0.1483 | 0.017273 | 0.05866 |
10 | 0.1350 | 0.014314 | 0.04861 |
11 | 0.1205 | 0.011404 | 0.03873 |
12 | 0.1055 | 0.0087417 | 0.02969 |
13 | 0.0915 | 0.0065755 | 0.02233 |
14 | 0.0800 | 0.0050266 | 0.01707 |
15 | 0.0720 | 0.0040715 | 0.01383 |
16 | 0.0625 | 0.0030680 | 0.01042 |